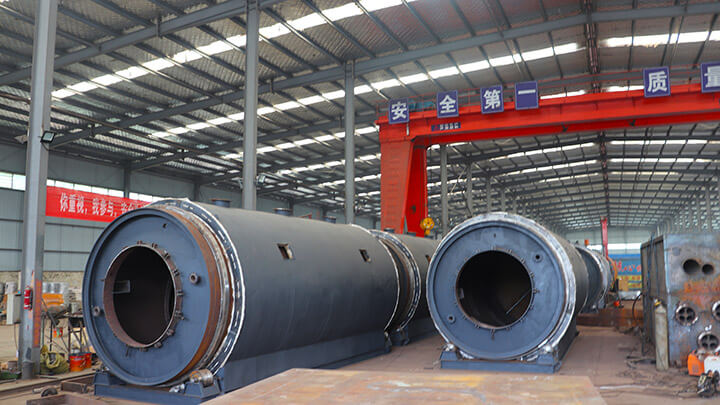
项目 | 详情 | |
输入原料 | 废轮胎、废橡胶、油泥、废塑料、医疗垃圾、城市生活垃圾 | |
终产品 | 燃料油、炭黑、钢丝、可燃气体 | |
型号 | 反应釜尺寸 | 产能 |
LES2000*6000 | 3 吨/天 | |
LES2200*6000 | 6 吨/天 | |
LES2200*6600 | 8 吨/天 | |
LES2600*6600 | 10 吨/天 | |
LES2800*6600 | 12 吨/天 | |
LES2800*8000 | 15 吨/天 | |
反应釜材质 | Q345R/Q245R/310S++锅炉板/不锈钢 | |
厚度 | 14 毫米/16 毫米/18 毫米 | |
重量 | 15吨-35吨 | |
功率 | 平均15千瓦/时 | |
冷却类型 | 循环水冷却 | |
所需面积 | 450-600平方米(宽:15米,长:30米-35米) | |
所需工人 | 3-4工人 | |
油密度 | 0.89g/cm3 | |
燃烧值 | 44.30KJ/KG | |
备注 | 可定制小型号试生产设备:100-500千克设备、1吨设备等 |
经过简单筛选有机物无机物分离等预处理工序,直接经皮带输送进入裂解设备,进料工段约2小时,每台设备进料10t左右。裂解炉内是一个持续升温的环境,炉体内部在4小时内升温至 200~300℃,此时裂解气开始处于稳定生成状态,接下来的 5~8 小时内温度缓慢爬升,当温度到达 450℃时,可认为塑料裂解已基本完成。
裂解过程中产生大量烟气,其成分主要包含重油(液态)、轻油(气态)、裂解气和少量水蒸气等,烟气经管道流入分汽包。新型废塑料裂解设备在分汽包内,重油下沉至渣油罐,通过油泵储存在储油罐内;气态成分经管道进入循环水冷却系统。在管道内冷却后的烟气分为液体和气体,其中气体为裂解气,液体为轻油和水的混合物。液体流入油水分离器,分离出的轻质油分经油泵进入油罐储存,少量含油废水经雾化后喷入裂解炉燃烧室作为燃料使用;裂解气经管道输送至裂解炉燃烧室作为燃料使用。经过8-10小时的裂解,除燃料油、裂解气外,裂解炉内还会生成炭黑。炉体停止加热后,项目采用空气冷却的方式,通过风机抽风不断带走炉体外壁热量,冷却工段持续时间约2小时。待炉体冷却至 200℃左右,操作人员打开一级、二级高温出渣机出渣。整个塑料裂解流程的总时间约为24小时。
1、直接加热:通过理论计算与实践数据,进行合理化设计,大大增加了炉体受热面积,从而有效的延长了设备使用寿命。微负压生产环境,全自动埋弧焊接技术,超声波无损检测。
2、八字拖轮支撑:本套设备采用新八字拖轮支撑,能够有效的分解支撑炉体的受力点,使裂解设备更加平稳、可靠的运行。
3、高温螺旋出渣系统:当裂解结束,温度控制在 200~220℃左右时,可打开一级、二级出渣系统清理炭黑。其特点:高温、密闭、自动出渣、清洁无灰尘等。
4、密封仓:炉体两端可设有密封仓,清洁无灰尘。
5、喷淋盘管冷却系统:国家实用新型技术,采用空气、喷淋水、冷却塔共同作用对可凝析油气循环冷却,其效果出油率高、油品质量好、使用寿命长、易清理。
6、废气回收系统:不可冷凝可燃气返回炉膛充分燃烧,不仅节省燃料,而且避免造成二次污染。
1、投入:
废塑料:750元/吨,750元*12吨=9000元。
工资:平均300元/人/天,300元*3人=900元。
电费:12小时用电共计约300千瓦,约300元。
燃料:目前很多省份已全面禁止燃煤,可以用轮胎油和天然气作为燃料,天然气限制条件比较多,建议采用轮胎油作为燃料,使用量约为400公斤。
每天总投入:9000元+900元+300元=10200元。
塑料油:按照40%出油率计算,12吨轮胎*40%=4.8吨轮胎油,燃料用400公斤剩余4.4吨。市场价2700元/吨*4.4吨=11880元。
2、炭黑:35%*12吨=4.2吨,市场价不低于300元/吨,4.2吨*300元/吨=1280元。
每天总产出:11880元+1280元=13140元。
3、净利润:
每天利润:每天总产出-每天总投入=13140元-10200元=2940元
每月利润:2940元*25天(每月按照25天计算)=7.35万元
每年利润:7.35万元*10个月(每年按照10个月计算)=73.5万元。